精益质量管理在产品和过程设计开发中追求产品的零缺陷;在产品制造过程中追求产品不合格率PPM为零;在产品实现全过程中追求使质量损失函数最小化的产品性能指数Ppk控制。
» 精益质量的理论
精益质量基于PDCA循环思想,认为任何质量改进项目的开展必须基于完善的制造过程控制系统的建立。企业应优先系统地建立制造过程控制系统预防质量问题,而非被动地解决质量问题。精益质量管理通过实施精益质量设计、精益质量制造建立起完善的制造过程控制系统,再通过精益质量改进来持续改进制造过程控制系统。
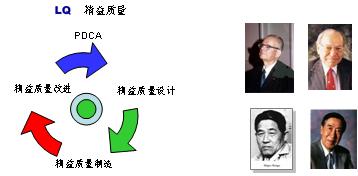
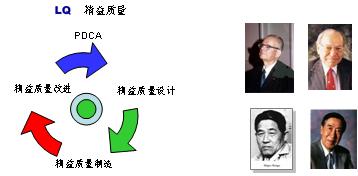
精益质量管理基于质量培训专家金舟军在精益质量中创新提出了“4sigma零PPM规律”, 即:制造过程的输出主要由少数的可控因子决定,真实制造过程变差则是受有限的不可控因子影响,所以稳定的制造过程输出的产品特性只是近似的正态分布,产品特性变差100%落入+4sigma至-4sigma范围内。精益质量管理理论认为:保持制造过程的稳定,制造过程精度达到4sigma, 产品不合格PPM即可为零。精益质量管理通过FMEA等无缺陷产品和过程设计开发工具实现无缺陷产品和过程设计; 通过SPC、防错和设备维护等现场控制工具维持制造过程的稳定,使制造过程精度保持在4sigma水平下,经济性地实现产品不合格PPM为零。

» 精益质量的两项质量指标
ISO国际标准化TC176的专家们对产品质量的定义是一组固有特性满足要求的程度,精益质量管理以顾客体验要求导向,提出了21世质量管理的两个质量指标:基于产品公差评价的不合格率PPM、产品质量损失函数评价指标—产品性能指数Ppk。
精益质量管理基于质量损失函数概念, 以顾客体验要求导向,除第一个产品质量评价指标-产品不合格率PPM外,还明确了与可靠性、返修率相关的第二个产品质量评价指标—产品性能指数Ppk。 产品性能指数Ppk是一个与产品质量特性变差分布和产品公差有关的指标,精益质量根据顾 客体验的质量损失函数敏感程度选择制造过程精度sigma水平,达到经济性的产品性能指数Ppk。
» 精益质量的益处
» 精益质量的益处
精益质量设计、精益质量制造、精益质量改进三阶段精益质量管理为企业提供既完整又有实施优先顺序的质量管理方法,依据企业状况循序渐进地实施质量管理,在不断取得效果中持续改进制造过程控制系统。
精益质量管理实现质量目标:产品不合格PPM为零、质量损失函数最小的目标,经济性地实现顾客对产品功能的当前和今后的持续满意。
» 精益质量的步骤
» 精益质量的步骤
精益质量管理按实施顺序分为精益质量设计、精益质量制造、精益质量改进三阶段,每一阶段都有相关的评审表,企业可根据评审表的评审结果决定本阶段的工具实施的优先顺序和是否进入下一阶段。
» PDCA循环与精益质量
PDCA循环由质量管理大师威廉.爱德华.戴明20世纪五十年代提出,PDCA包括:P策划、D实施、C检查、A改进四个阶段。精益质量管理的精益质量设计、精益质量制造、精益 质量改进三阶段是PDCA循环的应用,通过PDCA循环强调了实施精益质量设计、精益质量制造、精益质量改进的顺序和持续改进循环关系。
» ISO质量管理标准与精益质量
» ISO质量管理标准与精益质量
精益质量管理作为企业实施ISO900O系列标准的补充,帮助制造行业实施和保持,并持续改进质量管理体系中的产品实现过程。除非特别说明,精益质量所用的质量管理术 语与ISO9000:2000质量管理体系基础和术语是一致的。
精益质量管理还溶合吸收了ISO16949标准及其推荐的AIAG的质量工具FMEA、SPC、 APQP、PPAP、MSA手册的方法,并将它们分解、整合精益质量设计、精益质量制造、精益质量改 进中去。除非特别说明时,精益质量管理所用的质量工具术语与ISO16949、AIAG的术语是一致的。
